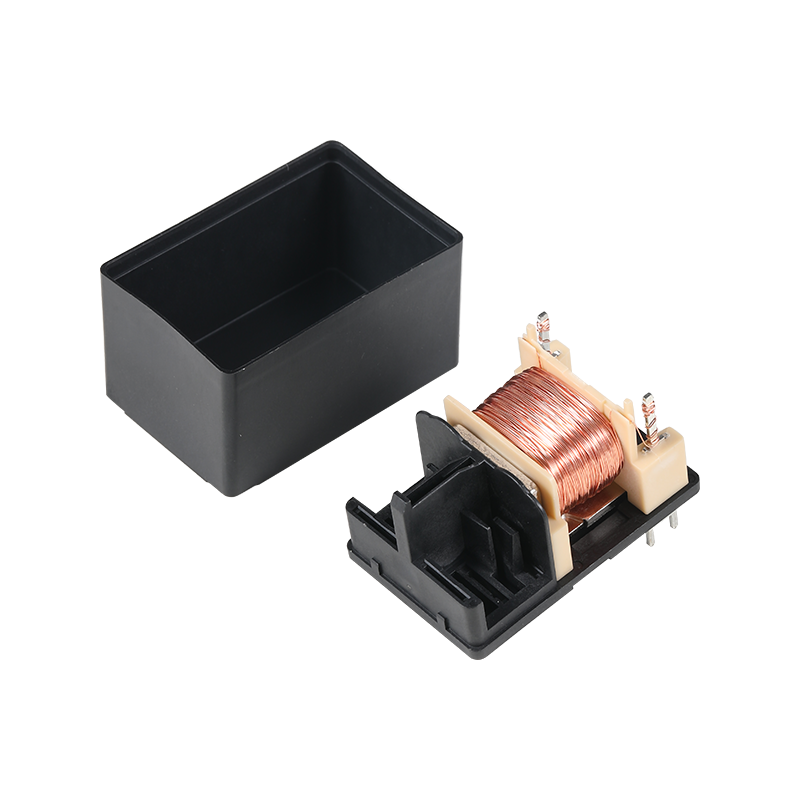
Пластиковая литья является широко используемым производственным процессом с приложениями, охватывающими различные отрасли, включая автомобильную, электронику и товары для бытовых товаров. Эти формы специально разработаны для формирования пластиковых материалов в желаемый конечный продукт, обеспечивая консистенцию и качество в массовом производстве.
Пластиковая форма корпуса - это тип подпрыгивающей формы, которая используется для создания чехлов или корпусов для различных продуктов. Эти формы обычно изготавливаются из высокопрочных металлов, таких как сталь или алюминий, чтобы выдерживать высокое давление и температуры, связанные с процессом литья под давлением. Плесень состоит из двух половинок - полости и ядра, которые работают вместе, чтобы сформировать пластиковую часть. Полость - это то, где впрыскивается расплавленный пластик, а ядро формирует внутренние признаки литого корпуса.
Пластиковые формы корпуса используются для производства широкого спектра продуктов, в том числе защитных корпусов для электронных устройств, корпуса для автомобильных деталей и контейнеров для промышленного использования. Дизайн и выбор материалов формы необходимы для производительности и долговечности конечного пластикового продукта.
Создание пластиковой формы корпуса следует нескольким ключевым этапам, которые включают:
Дизайн и прототипирование: единственный шаг в создании пластиковой формы корпуса - это проектирование продукта и самой формы. Дизайнеры используют программное обеспечение для компьютерного дизайна (CAD) для создания трехмерной модели корпуса, учитывая такие факторы, как простота сборки, поток материала и формулируемость. Прототипы часто создаются для проверки дизайна до создания конечной формы.
Изготовление плесени: как только конструкция завершена, следующим шагом является изготовление формы. Этот процесс часто включает в себя точную обработку, такую как фрезерование, бурение и EDM (обработка электрической разрядки) для создания полости и ядра. Затем плесень отполируется, чтобы обеспечить плавные поверхности и небольшие имгудуоны в конечном продукте.
Инъекционное формование: после приготовления плесени начинается процесс литья под давлением. На этом этапе пластиковые гранулы нагреваются до тех пор, пока они не таяют и не попадают в форму под высоким давлением. Расплавленный пластик заполняет полость, принимая форму корпуса. Как только пластик охлаждается и затвердевает, плесень открывается, а корпус выброшен.
Пост-обработка: в зависимости от требований продукта, для завершения литого корпуса могут потребоваться дополнительные шаги, такие как обрезка, отделка поверхности или сборка.
Преимущества использования пластиковых форм корпуса:
Точность и консизиона: пластиковые формы корпуса обеспечивают высокую точность и консизиона в производстве пластиковых компонентов. Это особенно важно в отраслях, где точность формованных случаев имеет решающее значение, например, в электронике и автомобильном применении.
Универсальность при выборе материалов: пластиковые формы корпуса могут вместить широкий спектр пластиковых материалов, включая термопластики и терморективы. Эта универсальность делает их подходящими для различных видов продуктов и отраслей.
Долговечность: формы предназначены для выдержания давления и температуры процесса литья под давлением, гарантируя, что они длятся для значительного количества циклов. Эта долговечность делает пластиковые формы корпуса надежным вариантом для долгосрочного производства.
Корпус пластиковые формы являются краеугольным камнем современного производства, что позволяет производству высококачественных, экономически эффективных пластиковых компонентов. Их способность производить сложные формы с высокой точностью, наряду с универсальностью для работы с различными материалами, делает их незаменимыми во многих отраслях.